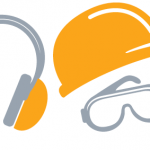
Safety Training on a Small Budget
One of your biggest obligations as an employer or business owner is to give your employees a safe working environment. They have the right, and you have the responsibility, to return home in the evening in the same condition as when they arrived at work in the morning.
But wait, you say, what about small businesses? How are we supposed to conduct stellar safety training like the big boys when we’re working on tight margins and a small budget? It can be done! That’s what we’ll explore in this issue of the ACT blog.
Small Doesn’t Mean Less Safe
For large, global corporations, local safety teams probably have access to mountains of training materials. They likely have a formal safety department, able to draw from additional corporate resources in their internal networks. But suppose you are a small business owner or manager. Your management staff might be a team of three or four people, trying to cover operations, finance, supply chain, customer service, and so on. There is no full-time safety manager; at best, everyone gets a small piece of that job. So how can you meet your responsibility of providing a safe workplace?
There are three primary drivers creating the need for safety training. These are:
- New employee safety training and orientation
- Job specific safety training
- Recurrent safety training (typically driven by federal or state regulatory requirements)
Let’s look at how each area can be accomplished with just a small budget.
New Employee Safety Training
All too often, new employee safety training consists of “follow Joe around and watch how he does things.” But what can end up happening is that Joe has found shortcuts and work-arounds to the way the job was designed; this may make it easier and quicker, but not necessarily safer, for him to complete the job. Perpetuation and even further enhancement of these habits will not help establish the cultural aspects of safety you need to develop.
While it may take a bit of time away from their day-to-day job, new employee safety training should always involve a member of the management team. First, it puts safety at a highly visible place in the organization, and shows the new employee that you really “walk the walk” about safety. While there is a time investment, in the big picture there is relatively little out-of-pocket cost following this approach.
Job Specific Safety Training
Your new employee safety training and orientation should feed seamlessly into this area of safety training. First, document your overall safety policy, and your specific location rules and regulations. Every employee should be aware of this document. For each job, or closely related family of jobs, the management team, in conjunction with the people actually doing the job, should develop a checklist of all the major requirements, learning, and tasks of a specific job. As an employee is going through job specific training, this checklist can be used to help with the training program.
At the end of the training program, this same checklist can be used as a test to ensure employee proficiency in safely performing the job. This should be ideally a combination of a written test of knowledge, followed by a hands-on demonstration of capability.
While preparation of job descriptions and checklists can seem like a daunting task, there is relatively little expense, and periodic updates will take little time investment.
Recurrent Safety Training
Typically, recurrent safety training is driven by specific state or federal regulatory requirements. It might also consist of a re-certification program for employees on the job, proving that, after a period of time, they are still competent to perform the requirements of the job.
Virtually every company faces the same requirements to perform this type of training. In this case, it is almost always more efficient to purchase training materials & programs rather than developing this yourself. These materials might be CDs or DVDs with both training and proficiency testing, or they could be written materials. Either way, there should be some level of customization to make them relevant to the specific workplace rather than completely generic. This could be as simple as preparing a short slide show linking the training to your situation.
Let Advanced Consulting & Training Help with Your Safety Training Programs
An effective safety program will always require an investment in management time and effort, but it does not require a heavy cost investment. Effective use of your own people and resources to develop a strong safety culture is easily in your grasp. Contact Advanced Consulting & Training today to find out how we can help your organization execute effective safety training programs without going over budget.