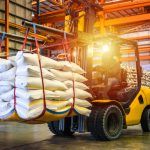
Five Essential Steps for Material Handling Safety
Is material handling a core component of your business? Are you concerned about maintaining safety standards when employees handle materials of varying size and weight as they go about their daily job duties?
Surprisingly, material handling is a source of safety issues and injuries in many workplaces. Let’s find out why that’s the case – and how to come up with an effective safety plan for materials handling.
Scope of Material Handling
Materials handling is a form of logistics movement that includes any process that involves the movement between vehicles, conveyors, store rooms, other forms of logistics support where employees are involved to some extent.
The extent of employee involvement will vary by operation and may include manual, automated, and semi-automated material handling events. The safety keys outlined below offer general guidance that would require tailoring for specific materials and logistics support scenarios.
An Effective Material Handling Safety Policy
The foundation for a safe workplace starts with policies and procedures that senior management must put in place. A comprehensive health and safety policy would include the appropriate level of guidelines on material handling and the associated employee training program.
A key portion of the policy would be the safety compliance activity that is essential for the business to operate. Most importantly, the policy would inform on the shared responsibilities of each employee in keeping the workplace safe.
These policies need to follow both the federal guidelines for occupational health and safety, as well as all provincial guidelines. Health and safety policies with respect to material handling need to address specific hazards including, but not limited to:
- Poorly maintained lifting devices
- Exceeding load limits on lifting devices
- Damaged racking and storage units
- Repetitive or overly heavy manual lifting, lowering, pushing, pulling or carrying loads
- Handling materials while on a ladder or step stool
- Being stuck between materials
- Falling materials that are improperly stored
- Incorrectly using securing devices on materials
- Collisions with moving equipment
Since the materials that are handled in the workplace on a daily basis can vary widely in size, shape, weight, and quantity, a safety policy for material handling will look very different from business to business. Each one needs to have a custom tailored policy to properly protect their employees who handle materials for their job.
Safety Training for Material Handling
There are employee safety risks involved with material handling in distribution centers, warehouses, shop floors and loading docks. The mitigation of safety risks starts with proper training in awareness, procedures and safety equipment.
Safety training is mandated for any new employees involved with lifting, carrying, loading or transporting materials in any form. In addition to new hire training, the safety risks and potential safety compliance rules may require re-training on an annual basis or some other regular time interval.
Material Handling Safety Procedures
The day to day handing of materials continues free of accident or injury when safety procedures are consistently followed. Procedures start with awareness of the specific material handling risks involved and the proper safety equipment for the situation. Procedures would cover the types of material, and the conditions of the work area.
Is the work area free of obstacles? Is there adequate lighting? Other procedures would cover the number of employees involved with specific handing events and the proper safety gear for the task.
Here’s a list for safely lifting and moving materials:
- Maintain the correct posture: avoid bending over and keep lifts close to the body
- Lift in a careful, deliberate manner and avoid any sudden lift movements
- Never lift materials from a sitting position, or twist to pick up a heavy object
- Use the correct grip on objects; lifts should be shoulder high and with full grasp of the hands
- Get assistance from co-workers to avoid successive lifts of heavy objects
- Always make use of conveyors, slides or other devices, to avoid unnecessary lifting or pushing of objects
- Always go around a blocked pathway, never step over an obstacle while carrying material
- Maintain a clear line of site; objects should not block vision; lift only where there is sufficient lighting
- Whenever possible; reduce load sizes, adjust bulky objects to ease movement
- Regularly stretch back and leg muscles during the day and keep in good physical shape
These are useful if posted and/or included in safety training manuals and modules.
How ACT Can Help with Your Material Handling Safety Training Needs
Safety for material handling gear means the proper fit and use of personal protection, to include, eye-protection, steel toed boots, other personal safety equipment.
Material handling safety equipment included the proper tools should be used in moving material. This would include the proper use of loaders, conveyers, forklifts and other aids to safely move material.
A company’s day to day operation and its customers are dependent on efficient logistics, and the employees involved must be trained and equipped to consistently work safely in meeting the material handling requirements of the business.
Knowing the Proper Safety Equipment to Use for Material Handling – And Its Proper Use
An safety plan for materials handling is part of an overall safety program for any organization that is involved in material handling.
Contact us today to find out how Advanced Consulting & Training can help you make, implement and execute a material handling safety plan.