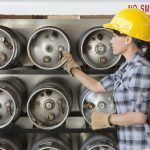
Material Handling: Reducing Workplace Incidents When Handling & Moving Materials
Material handling is a vital component for many businesses, ensuring a flow of parts through the workplace and for distribution channels. That’s why it’s crucial to conduct material handling in a safe and efficient manner. If not, the hazards of material handling pose a potential risk to the health and safety of your staff.
Today we’ll explore how to train for and conduct material handling to achieve workplace safety, covering the roles for various stakeholders including employers, supervisors and employees.
What are some of the risks involving material handling? How can you mitigate these risks?
Employers and supervisors are responsible for protecting workers from the hazards of material handling. While nobody can guarantee 100% safety in every instance, managers and supervisors (and the organization as a whole) are held accountable to industry and regulatory standards, and are expected to perform due diligence in overseeing workplace safety.
Material handling is a prime example of the inherent risks in workplace safety. Beginning with awareness and continuing with a proactive approach to training and prevention, supervisors and managers can work with staff to create a safe working environment for material handling.
Some of the hazards in material handling include:
- Workers being hit by materials, caught between them or in pinch points
- Exceeding load limits
- Falling caused by improperly stored materials
- Poorly maintained lifting devices
- Damaged racking & storage units
- Material handling whilst on ladders, stools, etc.
- Incorrectly cutting ties or other means of securing
As you can imagine from all of these (and there’s more!), injury can occur quickly (and significantly) if proper material handling guidelines and systems are not followed.
That’s why it’s important to have a clear training program in place, along with monitoring, evaluation and regular communication.
What are the roles of employers, supervisors and employees?
To ensure a safe workplace for material handling, it’s good for each party to know their roles in the process. These are set out by the Occupational Health & Safety Act (OHSA).
Employers
- Provide information, instruction & supervision
- Perform due diligence to prevent injury from material handling
- Make sure that equipment and facilities are safe and in working order
Supervisors
- Ensure that workers comply with OHSA regulations
- Communicate with workers about potential risks and any specific known issues (both verbally and in writing)
- Perform due diligence to prevent injury from material handling
- Make sure that equipment and facilities are safe and in working order
(You can see that Employers and Supervisors share overlapping roles & responsibility)
Workers
- Operate equipment and perform tasks in a safe manner
- Perform duties in compliance with OHSA regulations
- Report hazards and OHSA violations to supervisor or employer
For more on Regulations for Industrial Establishments, please see the OHSA page, covering “safe lifting, moving and storage of materials… and safe maintenance & operation of lifting devices, cranes and other equipment.”
Want to make sure your staff are properly trained on material handling, including forklifts, scissor lifts and more?
As you can see, a proactive approach to safe material handling is vital for your business. If you have questions or want to know more about how a training course can help you implement a proper material handling safety program, Advanced Consulting & Training would be happy to discuss this with you. We offer training in:
… and more!
Contact us today to find out how Advanced Consulting & Training can help you!