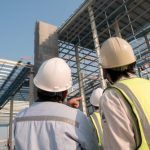
Best Approaches to Workplace Safety Audits for the New Year
Preparing your workplace for the New Year involves several practical steps for increased output.
A detailed workplace safety audit is essential for your business to reach its full potential.
What is a Workplace Safety Audit?
Workplace safety audits are in-depth examinations of an existing firm’s safety framework.
These audits focus on ensuring your present safety procedures are up to date and meet (or exceed) the company’s goals.
Safety audits reveal loopholes in an existing workplace safety framework, providing an opportunity for improvements. Hazard and risk identification is another focus of a professional workplace safety audit.
Essential Questions a Safety Audit Should Answer
Here are four essential questions every effective workplace safety audit should answer.
- Does the audit encompass every industry and regulatory practice available?
- Is the current safety system compliant with professional standards?
- Are employees gaining useful knowledge from training programs?
- Can employees respond to an accident with the training programs available?
If you find that your current workplace safety audits don’t address these points, it’s time to revamp the process!
Stages of a Professional Safety Audit
First stage: Audit planning
Before starting the audit, get information across to staff members in possession of essential records, procedures, and documents.
These documents are integral to your audit’s success.
If any audit has happened since the company’s inception, review all the information on these past assessments.
Also, determine a timeline for the audit and the scope of your investigation.
Second stage: Information gathering
Employee knowledge
- Gather relevant facts on the safety procedures your firm currently operates on
- Compile information on knowledge of safety procedures from management and staff
- Determine if there are personnel assigned to monitor adherence to safety procedures
Existing program review
- Compare existing safety program with industry requirements
- Assess employee knowledge of key safety elements (through questionnaires, interviews, etc.)
- Confirm if an effective safety training and re-training program is available for employees
Equipment and process assessment
- Investigate the state of PPE used in the facility
- Find out if there are any shortages of equipment and training
- Ascertain if accident response and prevention equipment are functional and up-to-date
Third stage: Findings review
After all processes get reviewed, detail a comprehensive report of your findings. Summarize these findings and provide simple answers to the questions outlined above.
Note shortcomings in the existing safety process after answering the four questions above at this stage.
Fourth stage: Safety audit recommendations
Make your recommendations for each deficiency in the company’s existing safety apparatus.
Final stage: Reparative procedures and results publishing
Based on recommendations from the audit, a reparative procedure should proceed on safety processes that fall short. And a detailed record of each step in this process should be reviewed and filed for future use.
How Advanced Consulting & Training Can Help
At Advanced Consulting & Training, a leader in workplace safety training in Ontario, we offer workplace safety training programs at your workplace or in one of our safety training classrooms.
We also offer a comprehensive safety consulting program that covers supervisor and manager due diligence. ACT has a successful track record of working with a variety of companies and workplaces to ensure that they are meeting or exceeding their manager due diligence.
Contact us today to find out more about how ACT can help your company or organization be a safer workplace through workplace safety audits.