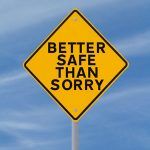
Identifying Types of Hazards in the Workplace
The process of identifying workplace hazards is an important step in assessing safety risks and planning.
It’s not just hazardous materials in the workplace that we’re talking about, but any object or condition that could potentially have a harmful impact on the course of regular operations or the day-to-day work of your employees.
That’s why it is essential to have a proactive approach when it comes to workplace hazards. Find out how to do just that in this edition of the ACT blog.
What Types of Hazards Might Be Lurking in Your Workplace?
Types of hazards vary by the conditions and activity specific to different work locations.
Any workplace condition that could lead to an injury must be identified.
As examples, injuries can occur when handling hazardous materials – or even handling any material incorrectly.
A complete assessment of the hazard types should be completed on a regular basis; as well as any time there is a change in workplace conditions that may introduce the potential for injury.
An effective workplace safety plan is critical to:
- mitigate potential harm to employee health
- reduce the costs to the business of compensation claims
- and avoid the morale hit that often accompanies a serious workplace injury
The plan starts with a hazard assessment. Next steps are to identify the workers who could be at risk and to develop a mitigation plan to avoid and/or minimize hazard risks.
Workplace Hazard Classification
Any workplace condition that can lead to an injury can be classified as a potential hazard related to chemical, biological, physical or ergonomic factors.
It is important to start out by properly categorizing the potential hazard risks to conduct an effective assessment and then to record key findings.
Assessment results provide a deeper understanding of the risks and help the team work through the procedural steps to avoid workplace injuries. The process of risk identification should involve management leads and the workers involved.
Another classification level to apply towards hazard identification is a type of root cause analysis for actual or potential errors. There should be an evaluation of the risk of human error for the potential of a serious hazard condition.
Are there situations where at risk behavior or even reckless worker behavior can lead to a hazard? It is necessary to consider these other cause factors in a hazard identification effort to ensure plans account for a range of possible risks.
Proper classification is essential to effective safety planning.
Proactive Approach to Workplace Hazard Identification and Mitigation
An enterprise safety program should include an approach that recognizes, in advance, the potential for injury in the workplace.
This is a continuous improvement approach that should be promoted and encouraged in all areas of the workplace.
This level of vigilance is especially necessary in an environment that is in constant change.
Common examples of proactive hazard identification would include spotting:
- improperly stacked pallets
- an electric cord with exposed wiring
- wet floors
- or any condition that may cause a workplace injury
The proper identification of these seemingly minor hazards is important to take the correct procedural steps to remove or minimize the risk.
The enterprise training and safety communication should encourage all employees to take a proactive approach to identify safety hazards.
Final Notes on Workplace Hazards – and how ACT Can Help
Workplace safety training manuals should be “living documents” that incorporate hazard identification input and safety feedback from staff across the workplace.
Other identification input should come from the results of regular safety inspections.
Workplace hazard identification is an important component in the overall health and safety plan for every workplace.
Contact us today to find out more about workplace hazard management and training programs.