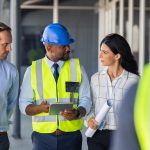
Different Types Of Hazards In The Workplace
Hazards in the workplace are inevitable; no working area is completely and totally safe. There are always measures that can reduce the risks or mitigate the effects of the hazards but the best way to avoid them is to know about them.
Hence the team at Advanced CT would like you to know about the different types of hazards in the workplace.
Physical Hazards
Hazards in the workplace can be in the very environment where employees work. Factors in said working space that can harm employees include temperatures, noises, chemicals, and toxic substances.
Extreme temperatures can be deadly in the workplace. Employees could suffer from heat stroke, hypothermia, and other related illnesses. To prevent this, appropriate ventilation and temperature control systems should be installed in the workplace. If necessary, employees should receive protective clothing when the situation calls for it.
Chemicals may be necessary for some workplaces but exposure to toxic ones can create severe health issues. Known issues associated with toxic chemical exposure include chemical burns and respiratory problems. To combat this, employees should be provided with the necessary PPE to eliminate exposure to toxic chemicals. Also, the ventilation of the workplace needs to be excellent to ensure toxic fumes aren’t trapped and breathed in later. Furthermore, chemicals should be stored and labelled properly to avoid errors in handling and usage.
Loud noises in the workplace can also negatively affect employees. The decibel level and duration may vary but prolonged exposure to noise over 85 dB (decibels) has been shown to cause hearing loss. They can also lead to issues like tinnitus, hyperacusis, and other hearing-related illnesses.
Ergonomic Hazards
Hazards in the workplace don’t have to be immediately obvious. They can be subtle and hidden like ergonomic hazards are. Factors that contribute to these types of hazards include bad posture, repetitive motions, and inadequate lighting. The effects of ergonomic hazards lead to serious musculoskeletal disorders.
Poor posturing occurs from holding bad positions when standing or sitting for extended periods. These can create strain in the joints and muscles, leading to misaligned spinal cords, compressed internal organs, reduced circulation, and other effects. Providing adjustable seating equipment to accommodate better postures and encouraging regular breaks will serve to mitigate the effects of these types of hazards.
Actions that are repeated in a similar way multiple times during the course of the workday are classified as repetitive motions. These include tasks like assembly line work and typing. These can lead to strain injuries like carpal tunnel syndrome. Encouraging regular breaks and giving training on the proper use of equipment can help mitigate the effects of these repetitive hazards.
Bad lighting in the workplace forces employees to strain their eyes when working. This can lead to headaches, migraines, reduced seeing ability, and other related eye illnesses. This can be resolved by ensuring that the work environment is adequately well-lit.
Safety Hazards
Hazards in the workplace can also be a result of the techniques, regulations and other related factors that directly affect an employee’s safety. Some of these factors include a lack of proper training, poor maintenance of equipment and poor safety practices. Without the right measures in place, these hazards can lead to accidents that cause fires, explosions and severe, if not traumatic, harm to employees. Also, the workplace will be ill-equipped to handle the resulting fallout from the accident.
Employees need training in the correct use of various machinery and equipment in the workplace. Without this training, the likelihood of accidents and injuries increases drastically. As such, the training of employees should be a top priority.
The maintenance of workplace equipment should be carried out on a regular basis. This will ensure that the equipment performs optimally and any issues are detected before they get too serious. Without regular maintenance, the chance for equipment failure increases and the damage that can result from said malfunction becomes greater.
Effective safety procedures should be put in place to ensure that any accidents or emergencies can be handled properly. Furthermore, the procedures need to be reviewed and updated regularly to stay relevant and effective and the employees need to be aware of them.
Advanced CT – Leaders In Occupational Health and Safety
Knowing about hazards in the workplace is the first step in handling them. With the right training and methodology, the workplace can be a safe environment for all employees.
Please contact us if you for the best consultation and training services available. Advanced CT has provided prompt and effective workplace safety solutions since our inception in 1998. All our safety programs are backed by credentials and can be delivered in person or online for your convenience.